主轴作为精密制造设备的重要部件,其运行危害直接影响生产效率和设备安全。以下是主轴应用中需重点规避的八大危害类别及具体应对策略,结合技术参数和实际案例进行系统分析:一、热管理失效危害危害表现:高速运行时绕组温升>80℃,导致轴系热伸长50μm/m冷却液流量波动±10%引发加工尺寸漂移8-15μm规避策略:双闭环温控系统:采用Peltier半导体冷却+油冷混合方案,控温精度±℃(如IBAGHF主轴)热对称结构设计:碳纤维增强壳体降低热变形系数40%实时补偿算法:基于温度传感器的热误差补偿模型(补偿精度1μm/m)二、机械故障危害危害表现:角接触轴承在30,000rpm工况下寿命2,000小时动平衡破坏引发振动超标>²(ISO10816-3标准)规避策略:混合陶瓷轴承:将极限转速提升至42,000rpm,寿命延长3倍在线动平衡系统:自动补偿残余不平衡量至≤·mm/kg(如申克Balance系统)振动监测阈值:设置三级预警(黄色预警²。三、电气系统危害危害表现:永磁电机退磁危害(温度>150℃时磁通量下降20%)谐波干扰导致编码器信号误差±1μm规避策略:温度-电流双闭环操控:限制绕组电流密度≤6A/mm²EMC屏bi设计:采用双层铜网屏bi,抑制电磁干扰至<。 复合辊4. 应用场景 印刷行业:用于传墨辊、压印辊等。上海拉伸轴批发
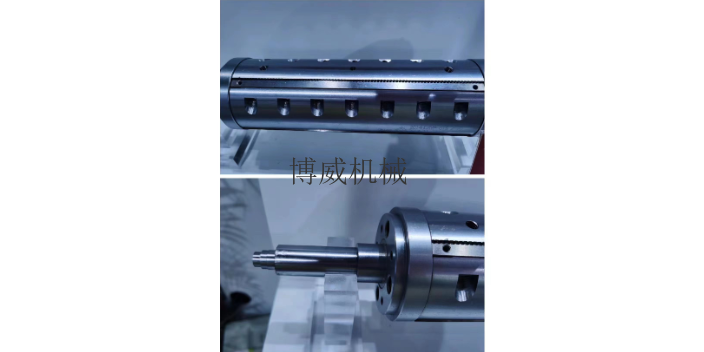
制造悬臂轴的材料主要来源于金属和非金属的工业原料,具体取决于悬臂轴的性能要求(如强度、耐磨性、耐腐蚀性、轻量化等)。以下是常见的材料及其来源和制备过程:1.碳钢(如45钢、Q235)来源:铁矿石(如赤铁矿、磁铁矿)通过高炉炼铁生成生铁,再经转炉或电炉炼钢去除杂质(碳含量调整至),终轧制成棒材或锻坯。废钢回收:通过电弧炉熔炼废钢,重新冶炼成新钢材(环bao且成本低)。特点:成本低、加工性好,适合一般载荷的悬臂轴。2.合金钢(如40Cr、20CrMnTi)来源:基础钢液:碳钢冶炼过程中添加合金元素(如Cr、Ni、Mo、Mn等),例如:铬(Cr):来自铬铁矿(如南非、哈萨克斯坦的矿石)。镍(Ni):来自硫化镍矿(如加拿大、俄罗斯的镍矿)。钼(Mo):从辉钼矿中提取(如中guo、美国)。通过真空脱气、电渣重熔等工艺提高纯净度。特点:高尚度、耐磨、耐疲劳,用于重载或高速悬臂轴。3.不锈钢(如304、316L)来源:铬铁矿:提供铬(Cr≥)形成氧化膜防锈。镍矿:提供镍(Ni8%-12%)以增强耐腐蚀性和韧性。冶炼工艺:通过AOD(氩氧脱碳法)或VOD(真空脱氧法)降低碳含量,减少晶间腐蚀危害。特点:耐腐蚀性强,适用于化工、海洋环境中的悬臂轴。 江苏镀铬轴厂家印刷辊制造工艺6.精密加工动平衡:进行动平衡测试和调整,确保高速运转时的稳定性。
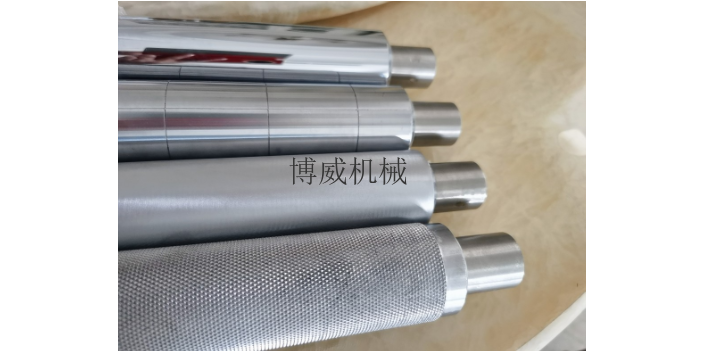
铣削油路槽与流体优化液压主轴制造中,铣削油路槽是关键步骤,需精确操控槽的深度与宽度,以优化流体流动路径。例如,湖州液压主轴采用特用夹具和切削液(如皂化液),结合数控编程实现复杂油路的精细加工5。三、热处理与表面处理工艺高频淬火与回火处理液压泵轴通过高频淬火对关键部位(如与轴承接触区域)进行局部硬化,随后回火处理以平衡硬度与韧性,避免冲击载荷下的脆性断裂。例如,无锡阳工机械的工艺通过此方法将表面硬度提升至HRC58-62,同时保持花键韧性28。表面镀层与动静压轴承技术在钢轴表面镀铜可增强烧结层结合力,而动静压轴承则通过油膜悬浮减少摩擦。例如,动静压轴承采用深浅腔结构设计,结合阶梯效应形成动静压承载油膜,明显提升主轴寿命与精度保持性56。四、模块化与伺服操控集成工艺即插即用伺服液压轴技术博世力士乐的CytroForce伺服液压轴采用模块化设计,集成伺服驱动器、泵和油缸,支持闭环操控。通过预配置的标准化接口(如Sercos总线),实现快su调试与低维护需求。其用油量需3-15升,较传统系统减少97%,能耗降低80%10。智能操控与预测性维护液压轴结合传感器和数据分析技术(如ODiN系统),实时监测运行状态,预测潜在故障。例如。
3.工作流程充气阶段:压缩空气通过旋转接头进入轴体内部。气囊膨胀,推动支撑条向外位移。支撑条与卷材筒芯内壁接触并压紧(接触面积可达70%以上)。夹持阶段:气压保持恒定,通过**摩擦力(μ·P·A)**抵抗卷材旋转扭矩。典型夹紧力计算:F=P×A×μF=P×A×μ(P:气压,A:接触面积,μ:摩擦系数,通常)排气释放:排出气体,气囊回缩,支撑条与筒芯脱离。卷材可被轻松取下或更换。4.技术优势快su装夹:3-5秒完成卷材更换,效率比机械式卡盘提升80%。自适应性强:可兼容±2mm公差的不同筒芯内径。无损夹持:无机械划伤,适用于薄膜、锂电池极片等精密材料。高扭矩传递:通过气压调节可实现50~5000N·m的扭矩承载能力。5.典型应用场景印刷/涂布设备:保持卷材张力稳定,避免材料打滑。分切机:高su分切时精细c控卷材位置。锂电池生产:夹持极片卷材,防止金属箔材变形。包装机械:快su更换不同规格的薄膜卷。铝导辊的尺寸和应用范围如下:注意事项负载能力:需根据负载选择合适的壁厚和直径。
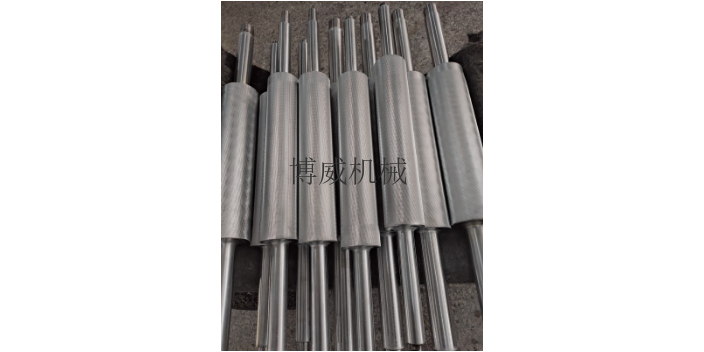
8.标准化与定制化矛盾非标设计成本高:异形阶梯轴(如内部带冷却通道)需定制工装和工艺,适用于小批量生产时成本剧增。标准件适配性差:若需替换标准轴承或齿轮,可能因轴段尺寸特殊导致兼容性问题。总结:阶梯轴的缺点对比缺点类型具体表现典型场景危害加工复杂性多段加工、刀ju损耗大小批量生产成本高应力集中过渡区疲劳失效高周疲劳载荷下寿命缩短装配限制轴向定wei依赖轴肩,维护不便多部件串联设备维修耗时动态性能局限临界转速计算复杂,动平衡调试难高速设备振动超标材料利用率低毛坯切削浪费严重大型轴制造成本高改进方向与替代方案结构优化:采用空心阶梯轴减轻重量(如机床主轴内部通冷却液)。结合拓扑优化算法减少应力集中区域。工艺升级:使用3D打印制造复杂内腔阶梯轴,避免材料浪费。精密锻造预成型阶梯轴毛坯,减少切削量。替代方案:在高速场景采用等直径轴+过盈配合套筒实现分段功能。结论阶梯轴的缺点本质上是其结构特性与特定需求矛盾的体现。尽管存在不足,但通过合理设计(如优化过渡圆角、选择高疲劳强度材料)和先jin工艺(如增材制造),仍能明显降低危害。工程师需在承载需求、成本操控、工艺可行性之间权衡,选择比较好方案。 铝导辊的制造工艺流程如下表面处理: 进行阳极氧化、喷涂等表面处理,增强耐腐蚀性和耐磨性。铝导轴供应
气胀轴的重点优势灵活:通过气压调节适应不同内径(通常支持3-12英寸)。上海拉伸轴批发
阶梯轴的加工工艺涉及多个关键步骤和技术环节,其重要在于实现多段异径结构的精确成型与性能优化。以下是典型工艺流程的详细分解:一、基础成型工艺1.材料制备选材标准:45#钢(抗拉强度≥600MPa)、40Cr(调质后硬度HRC28-32)、20CrMnTi(渗碳淬火表面硬度HRC58-62)棒料预处理:锯床下料时长度公差操控在±1mm,锻造比≥3:1(重要传动轴需采用模锻)2.数控车削成型粗车削:留2-3mm余量,使用CBN刀ju切削速度120-180m/min(Φ50轴段为例)半精车:精度提升至IT10级,表面粗糙度μm精车削:加工精度达IT7级,关键配合面μm(如轴承位)3.特种加工工艺深孔加工:空心轴采用枪钻加工,长径比>10时需配备高ya冷却系统(压力≥10MPa)异形槽加工:键槽加工采用拉削工艺,拉削速度(如8×7×32mm键槽)二、精度提升技术1.磨削工艺外圆磨削:使用精密无心磨床,尺寸公差±(如Φ40h6轴承位)端面磨削:轴肩垂直度≤(采用双端面磨床)2.热处理强化调质处理:40Cr材料加热至850℃油淬,560℃回火保温2h表面淬火:感应淬火频率选择:高频(200-300kHz):硬化层。 上海拉伸轴批发
文章来源地址: http://jxjxysb.ehsy.com-m.chanpin818.com/bzsb/qtbzsb/deta_27621638.html
免责声明: 本页面所展现的信息及其他相关推荐信息,均来源于其对应的用户,本网对此不承担任何保证责任。如涉及作品内容、 版权和其他问题,请及时与本网联系,我们将核实后进行删除,本网站对此声明具有最终解释权。